La historia de una rampa se volvió una fresadora
Detalle BN6
- Inicio
- La historia de una rampa se volvió una fresadora
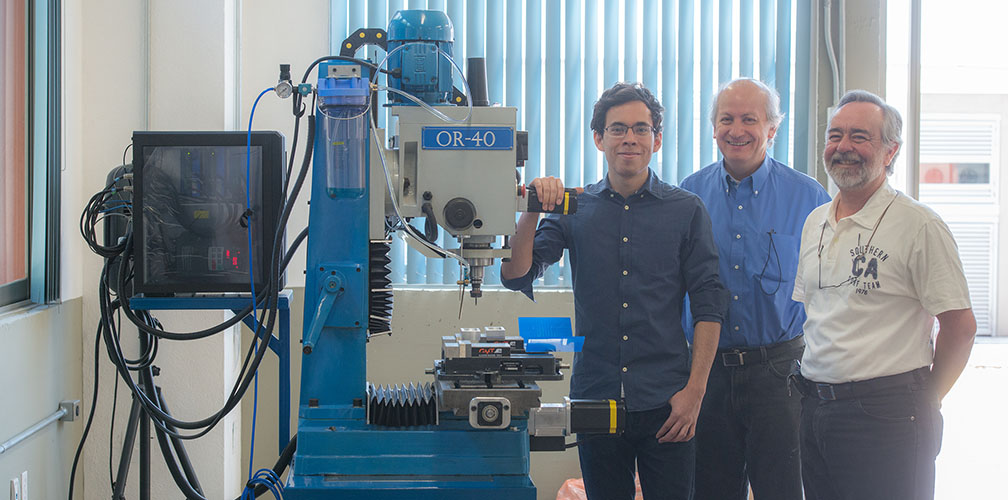
La historia de una rampa se volvió una fresadora
Dos empresarios y tres estudiantes de Ingeniería Electrónica diseñaron un aparato que no existía en el mercado, y que podría ser una solución para los pequeños talleres de torno.
Vanesa Robles
Esta es la historia sobre cómo el boceto de una rampa para sillas de ruedas se transformó en el invento de una fresadora computarizada. Sus protagonistas son los ingenieros Ramón Contreras y Jesús González, quienes el día de su retiro de la empresa Intel, en 2014, se encontraron por coincidencia y decidieron "hacer algo" juntos, para lo que luego contaron con la colaboración de un trío de estudiantes de Ingeniería Electrónica del ITESO: Daniel Solís, y Héctor y Érick Ortega, quienes fueron invitados a participar en el proyecto.
Uno de los resultados es una nueva máquina para torno con características que no existían antes. Se trata de una fresadora que, guiada por computadoras, puede generar moldes, prototipos y engranes de acero, cobre, acrílico y madera, entre otros materiales, para producir desde suelas de zapatos hasta piezas para naves aeroespaciales.
Otro resultado es la conjunción de Proyectos de Aplicación Profesional (PAP) interdisciplinarios en torno a Daptta, la empresa de Contreras y González.
Primero, la historia de la rampa.
Una de las primeras ideas que se les ocurrió a los ingenieros retirados fue un proyecto de movilidad para personas con limitación motriz, después de que Ramón Contreras vivió de primera mano la dificultad de trasladar a su padre sobre una silla de ruedas.
El problema comenzó cuando él y Jesús González decidieron comprar una fresadora de Control Numérico por Computadora (CNC) para hacer el molde de un prototipo de rampa. Costaba, en dólares, el equivalente a un millón de pesos. "Queríamos figuras complejas, difíciles de lograr, que no podíamos obtener con una máquina mecánica".
La investigación los llevó a enterarse de que, quizás antes del primer proyecto, tendrían que proponer una solución tecnológica para el torno.
"Hay talleres con máquinas convencionales, que quieren dar el brinco, pero el brinco es muy alto: un millón de pesos. Decidimos que tendríamos que tomar una fresadora manual y transformarla en una CNC", relatan.
A lo largo de su trayectoria, Contreras y González habían trabajado, por separado, en empresas de tecnología avanzada, como IBM y HP, respectivamente, y en Intel, al mismo tiempo. Sabían que parte de las estrategias y el éxito de estas firmas trasnacionales es la incorporación de estudiantes universitarios, quienes aportan ideas y favorecen los procesos de innovación.
Recurrieron al ITESO, donde los atendió Omar Longoria, coordinador de Ingeniería Electrónica. "Pensamos que no nos iban a hacer caso, pero una vez que expusimos nuestro proyecto, se nos abrieron las puertas de par en par", comentan.
Los años de experiencia de González y Contreras, y sus maestrías en la Universidad de Stanford, California, y en el Centro de Investigación Científica y de Educación Superior de Ensenada, Baja California, respectivamente, les han dado los conocimientos para saber que los estudiantes de las instituciones mexicanas están en el mismo nivel competitivo que los de las universidades más prestigiosas del mundo. Por algo, recuerdan, de los tres centros de desarrollo tecnológico que Intel tiene en el mundo uno está en la Zona Metropolitana de Guadalajara.
Así, los estudiantes Daniel Solís, Héctor y Érick Ortega fueron una bocanada de aire fresco para el proyecto, que ahora trabaja en el Parque Tecnológico.
La misión era desarrollar una fresadora que tuviera la calidad de las más caras, pero con una producción de costo bajo. En el panorama estaban los aparatos europeos, de precisión muy alta y un costo mínimo de un millón de pesos. Y los aparatos chinos, que no son mecánicamente perfectos, pero sí más económicos. La solución surgió de ambos.
El equipo de nuevos empresarios y estudiantes tomó una mesa china, a la cual le pusieron piezas de calidad excelente y un control de sensores de alta definición, que detecta las imperfecciones de la mesa y, a través de algoritmos de software, corrige sus errores, para volverla perfecta.
La máquina se llama OR 40. Posee seis computadoras, de las cuales tres son de alta velocidad y un CNC código G, que es capaz de reproducir con exactitud el diseño de un prototipo digital en 3D, y que más tarde es interpretado por la máquina. Cuesta alrededor de 12 mil dólares, una cuarta parte del precio de las fresadoras de alta precisión que existen en el mercado. Es sencilla de operar y de mantener.
Está dirigida a los microempresarios que tienen talleres de tornos manuales y desean incorporar fresadoras CNC de precio accesible; a los empresarios que tienen las máquinas de un millón de pesos y quieren aumentar su producción, y a las escuelas que, con fines educativos, adquieren las CNC pero las tienen paradas, por temor a una descompostura.
A propósito de escuelas, durante todo el proceso Daniel Solís participó en el diseño electrónico y del CNC de la máquina. Hoy sigue trabajando con Daptta, después de casi dos años. Describe su experiencia como un "shock formidable", pues desde el primer día supo que, junto con sus compañeros, la labor no sería de cooperación, sino la responsabilidad entera de un proyecto de innovación. Eso implicaba aplicar la teoría en un proyecto real y, por supuesto, equivocarse.
En estos días, tres PAP del ITESO trabajan en torno de la empresa recién creada. Uno de ellos incluye a estudiantes de las ingenierías Mecánica y Electrónica, así como de Comercio Internacional; hay otro de Mercadotecnia, desde el cual salieron el nombre y la imagen de Daptta, y uno más de Derecho.
¿Y la rampa para sillas de ruedas? Parece que esperará un poco. Sólo un poco.
Noticia